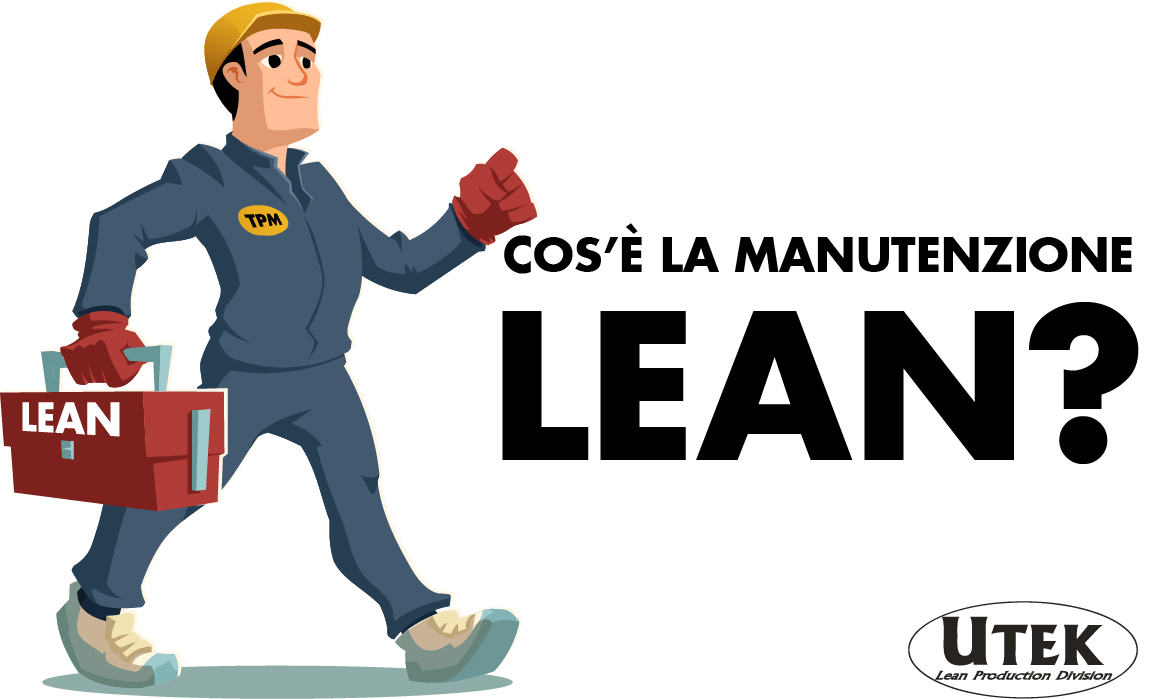
Indice dei contenuti
- La manutenzione è sempre necessaria
- Cos’è la manutenzione Lean o TPM?
- Cosa serve per integrare il metodo TPM?
- I pilastri della produzione snella TPM
- OEE e vantaggi TPM
- Quali sono dunque i vantaggi attesi dall’implementazione di una produzione snella TPM?
- Come migliorare questo processo di manutenzione
Manutenzione e Lean Production sono due aspetti che devono essere valutati in simbiosi, senza creare blocchi o compartimenti stagni. Per un motivo molto semplice: se dobbiamo ragionare in termini di efficienza e ottimizzazione dei processi interni non bisogna mai perdere di vista questo passaggio. Vale a dire quello che ti consente di mantenere ogni strumento utile alla produzione in uno stato di massima efficienza.
Nel corso dell’ultimo decennio, il pensare Lean ha spinto le aziende a focalizzare la propria attenzione sull’efficienza dei singoli processi per poter incrementare la produttività e redditività. Un prerequisito fondamentale per chi decide di abbracciare i principi della Lean Production è avere impianti funzionanti per poter evitare ogni forma di spreco, dai fermi produttivi agli infortuni da cattivo funzionamento dei macchinari.
Affinché tutto funzioni quando necessario, è importante procedere con una costante e corretta manutenzione svolta preventivamente, in grado di evitare problemi futuri a causa di sprechi.
La manutenzione è sempre necessaria
Questo è il punto di partenza per un'ottimizzazione concreta della manutenzione in ottica Lean Production:
Non è da considerarsi come tempo perso o fase da limitare, eliminare e ridurre. Perché ci sono macchine e attrezzature che hanno bisogno di attenzioni particolari. Sia per evitare guasti che per aumentare l'efficienza. In questo modo è possibile avere come riferimento la Lean Production.
L'attrezzatura che riceve la giusta manutenzione riesce a minimizzare i tempi di sosta inavvertita a causa di problemi tecnici, con relativo calo della produttività, e mantiene i ritmi definiti dalla tabella di marcia. Quindi bisogna sempre includere questi processi in quello che viene definita metodologia TPM.
Cos’è la manutenzione Lean o TPM?
La manutenzione snella (o Lean Maintenance) è un'operazione proattiva che prevede attività pianificate e programmate attraverso TPM.
Vale a dire Total Productive Maintenance. Questo metodo viene tradotto in Italia come manutenzione produttiva e ha uno scopo ben preciso: inserire la manutenzione in un processo virtuoso in grado di ridurre al minimo il tempo perso nelle soste dovute alle interruzioni che si verificano nel momento in cui viene ignorata la prassi necessaria a evitare che gli impianti si fermino.
Il TPM cerca d’individuare i problemi prima che accadano, utilizza questa ideologia per creare un’operazione più efficiente e semplificata tramite strategie di manutenzione sviluppate attraverso l'applicazione della logica decisionale centrata sull’affidabilità RCM praticate da team con metodi 5S, eventi kaizen e manutenzione autonoma. L'aspetto importante e che fa la differenza rispetto ad approcci differenti: c'è il coinvolgimento dell'intera struttura organizzativa. Non è solo un problema relativo a chi deve fare la manutenzione ma diventa un processo che chiama in causa il management e gli operatori perché punta ad assegnare responsabilità della manutenzione preventiva e ordinaria alle stesse persone che utilizzano l'attrezzatura.
TPM si basa sulle fondamenta 5S, ovvero un’organizzazione efficiente del posto di lavoro e l’utilizzo di procedure standard in grado di migliorare la sicurezza, la produttività, la qualità e l'atteggiamento stesso dei dipendenti.
Il primo obbiettivo del TPM è l'efficienza degli impianti per recuperare le perdite maggiori e realizzare risparmi in poco tempo. Il che vuol dire:
- Zero guasti imprevisti
- Zero difetti nei prodotti
- Zero incidenti
- Zero rallentamenti produttivi o interruzioni
Il TPM è un cambiamento culturale che mette a frutto i concetti della Lean Production rivedendo completamente la manutenzione degli impianti che può richiedere anni ma vale la pena investire sia per il prodotto finito sia per il coinvolgimento dei dipendenti.
Tra gli aspetti più importanti da considerare quando si parla di metodologia TPM c'è la fase predittiva. Ovvero, la manutenzione non viene considerata solo come un'azione da svolgere in un determinato momento deciso in linea teorica: si studiano i dati e si agisce di conseguenza, in modo da agire quando serve veramente.
Di conseguenza la manutenzione non si occupa solo di svolgere le azioni necessarie per il buon funzionamento ma raccoglie i dati sulla frequenza, natura e durata dei guasti, in modo da attuare un’attività di miglioramento.
In questo modo c'è un continuo aggiornamento dei canali necessari a capire come e quando fare manutenzione.
Cosa serve per integrare il metodo TPM?
Per riuscire in questo obbiettivo è necessario:
- Andare a rivoluzionare il pensiero delle persone, spiegando quanto sia importante ridurre sempre di più e in qualunque forma, i tempi di produzione per poter restare concorrenziali.
- Predisporre strutture organizzative orizzontali per snellire le decisioni e rendendole a valore aggiunto.
- Imparare a lavorare in team per poter reagire prontamente e nella maniera più corretta.
- Formare adeguatamente per poter intervenire con gli strumenti e le soluzioni più idonee.
Perché se l'obiettivo è quello di raggiungere il kaizen, vale a dire una perfezione in cui lo spreco si annulla, bisogna fare in modo che la fase di manutenzione sia trattata da non diventare una perdita in termini di tempo, risorse e produttività.
Quali sono i punti necessari per affrontare la logica della manutenzione in ottica Lean Production?
I pilastri della produzione snella TPM
Per procedere con l’implementazione del metodo TPM in maniera efficiente e per comprenderne i reali vantaggi, bisogna imparare a conoscere i suoi otto pilastri che ne creano le fondamenta.
Questi pilastri ne rappresentano i vari obbiettivi e forniscono un punto focale su come raggiungerli.
- Manutenzione autonoma: Questo è il concetto più rivoluzionario, le manutenzioni ordinarie generali della macchina come possono essere la pulizia, la lubrificazione, l'ispezione e altre semplici attività di routine sono normali operazioni che non richiedono l'esperienza del personale di manutenzione dedicato e dovrebbero essere gestite da coloro che lavorano quotidianamente e attivamente su tali macchinari o stazioni di lavoro. Ciò consente ai manutentori professionisti di occuparsi maggiormente di questioni più complesse e pone una maggiore responsabilità e coinvolgimento ai vostri operatori.
- Miglioramento Continuo: Il modo migliore per puntare a lavorare verso la perfezione del TPM sono i progetti incrementali. I progetti TPM non solo ti aiuteranno a raggiungere gli obbiettivi di miglioramento, ma aumenteranno il coinvolgimento dei lavoratori riunendo diversi gradi e competenze. L’efficienza di un progetto TPM ti aiuterà a dimostrare ai lavoratori il potenziale del metodo su ampia scala. Questi progetti possono essere stabiliti anche direttamente dai suoi membri che potrebbero aver notato qualcosa che necessità di manutenzione o modifica durante il loro lavoro quotidiano.
- Manutenzione programmata: Alcune manutenzioni escono dalle capacità degli operatori di linea e devono essere eseguite da professionisti pianificandole con cadenza periodica in base a fattori come tasso di guasti previsti, utilizzo, durata media e altro ancora. La pianificazione con largo anticipo deve servire a prevenire guasti inaspettati per evitare blocchi alla produzione. L'obbiettivo del TPM è avere solo un 10% di manutenzione reattive perché il restante 90%, devono essere manutenzioni preventive e autonome.
- Miglioramento della qualità dei processi: E' un tipo di manutenzione incentrato sulla capacità di rilevare tempestivamente problemi e difetti nel processo produttivo. Se gli operatori di linea si occupano di svolgere le attività di manutenzione base, il team potrà dedicarsi alla gestione della qualità del processo per migliorare l'efficienza complessiva della macchina. Se una macchina ha una lama usurata, ad esempio potrebbe non riuscire a eseguire un taglio netto, la gestione della qualità del processo richiederà al team di manutenzione di affilare o sostituirla. La pronta sostituzione evita prodotti difettosi o non conformi allo standard aziendale. A volte bisogna affidarsi all’ occhio esperto del manutentore, in altri casi potrebbero esserci parametri di sicurezza integrati nel macchinario stesso che non consentono una produzione quando viene rilevata un’anomalia.
- Formazione: Il TPM richiede un training obbligatoria prima di prendere parte al processo produttivo. Ad esempio se richiedi la manutenzione autonoma del primo pilastro dovrai assicurarti che gli operatori siano adeguatamente formati su come eseguirla.
- Ambiente e Sicurezza: Questo pilastro non è certo esclusivo del metodo TPM ma è altrettanto importante. La sicurezza e sempre la massima priorità sul lavoro. La salute e sicurezza giocano un ruolo preciso nel TPM. Gli incidenti e le conseguenti perdite di manodopera sono ovviamente uno ostacolo a un’efficienza produttiva. Ridurre al minimo gli incidenti significa avere meno tempo speso per attività senza valore.
- Il TPM non è solo per i processi produttivi, puoi migliorare anche l'efficienza nel settore amministrativo della tua azienda.
- Gestione di nuove attrezzature: Il TPM richiede un’attenta valutazione dei benefici che potrebbe portare l'acquisto di una nuova attrezzatura e le alternative possibili. In genere attività simili possono essere completate seguendo strade diverse, pertanto ci sono molti fattori da considerare prima di scegliere un nuovo macchinario. Quando si segue una metodologia TPM, è essenziale che il fattore da tenere in considerazione è la qualità della macchina. Acquistare macchine qualitative contribuirà a ridurre ulteriormente i fermi macchina. Quando si acquista una macchina il team dovrà creare una guida di manutenzione dettagliata per garantire che rimanga in perfette condizioni al più lungo possibile.
- Miglioramento attrezzature: Quando l’obbiettivo è limitare i tempi di fermo di una macchina è importante investire in miglioramenti che la rendono più affidabile. Non si tratta solo di svolgere i periodici aggiornamenti, si può anche trattare d'introdurre sistemi automatici, di sostituire componenti ormai obsoleti o in casi estremi l’intero macchinario.
OEE e vantaggi TPM
Uno degli strumenti fondamentali per misurare i risultati del Total Productive Maintenance è l’OEE dall’acronimo Overall Equipment Effectiveness, quel valore in grado di calcolare l’efficacia totale di un impianto. Misura l’efficienza dell’impianto mettendo in relazione tra loro l'indice di disponibilità, di performance e di qualità stesso dell’impianto. E’ possibile calcolare tale valore moltiplicando le seguenti percentuali:
Periodo di tempo nel quale i macchinari sono effettivamente funzionanti e utilizzabili in produzione
X
Efficienza dei macchinari
X
Tasso di qualità dei macchinari
Ipotizzando:
Tempo di utilizzo del 90%
Efficienza del 95%
Tasso qualità del 99%
Il nostro OEE sarà intorno al 85%
Con a disposizione queste informazioni e con un programma di manutenzione dettagliato per ogni macchinario, puoi avere dati sempre aggiornati sull’efficienza generale dell’impianto e dei singoli step di lavoro.
Quali sono dunque i vantaggi attesi dall’implementazione di una produzione snella TPM?
1. Maggiore efficienza degli impianti e delle attrezzature
2. Dati aggiornati sull’efficienza produttiva dell’intero impianto e delle singole fasi di lavoro
3. Manutenzioni predittive basate su programmi realizzati a monte del processo e basati su dati oggettivi e aggiornati
4. Coinvolgimento di tutti i dipendenti a ogni livello per il corretto funzionamento di tutti le parti
5. Manutenzioni standard gestite da team di lavoro formati e sempre presenti sul campo
Il programma TPM per una Lean Production è un meccanismo che può fare la differenza tra un’azienda che produce e una che lo fà in modo efficiente e senza sprechi.
Meno sprechi sono sintomo di meno spese e più entrate, benessere psico fisico dei dipendenti e aumento del valore per il cliente.
Come migliorare questo processo di manutenzione
In primo luogo, come suggerito nei passaggi precedenti, si usano i dati statistici. Cosa fare e quando muoversi, questi parametri aiutano a creare un processo di manutenzione migliore e adeguato alle necessità. Ma c'è un altro punto da considerare: la diversificazione delle attività. Ad esempio esiste una manutenzione pianificata che segue i processi studiati e stabiliti, poi ci sono gli studi per attivare una manutenzione autonoma: meglio preferire macchine che gestiscono senza bisogno dell'intervento umano le varie attività.
Questo punto si allinea con la necessità di avere macchine che prevedono una manutenzione più rapida e che magari non chiamano in causa il blocco delle attività, o che possono essere gestite mentre si effettuano altre operazioni.
Questo è un aspetto interessante che si riscontra anche nella metodologia SMED: studiare i tempi di setup in modo da ridurre i tempi necessari per cambiare settaggio alla macchina.
La manutenzione virtuosa permette di creare tutto questo, ma soprattutto pone le basi della produzione snella e si inserisce a pieno titolo nella tecnica delle 5S. Tutto questo avviene anche grazie alla strumentazione e alle dotazioni migliori che si allineano con l'idea di avere minor bisogno di manutenzione.
- SMED Trolley
- Lifter posizionatori
- Pannelli forati porta attrezzi
- Marcatura del pavimento
- Identificazione dei materiali
- Tool Organizers
- Identificazione scaffalature
- Porta etichette adesive o magnetiche
- Tool Shadow Boards
Manutenzione e Lean Production devono essere considerate due facce della stessa medaglia:
bisogna scegliere la strumentazione giusta per ridurre tempi di ottimizzazione e studiare tutti i percorsi necessari per ridurre tempi, risorse e sprechi. Da dove iniziare? Contattaci su info@utekvision.com