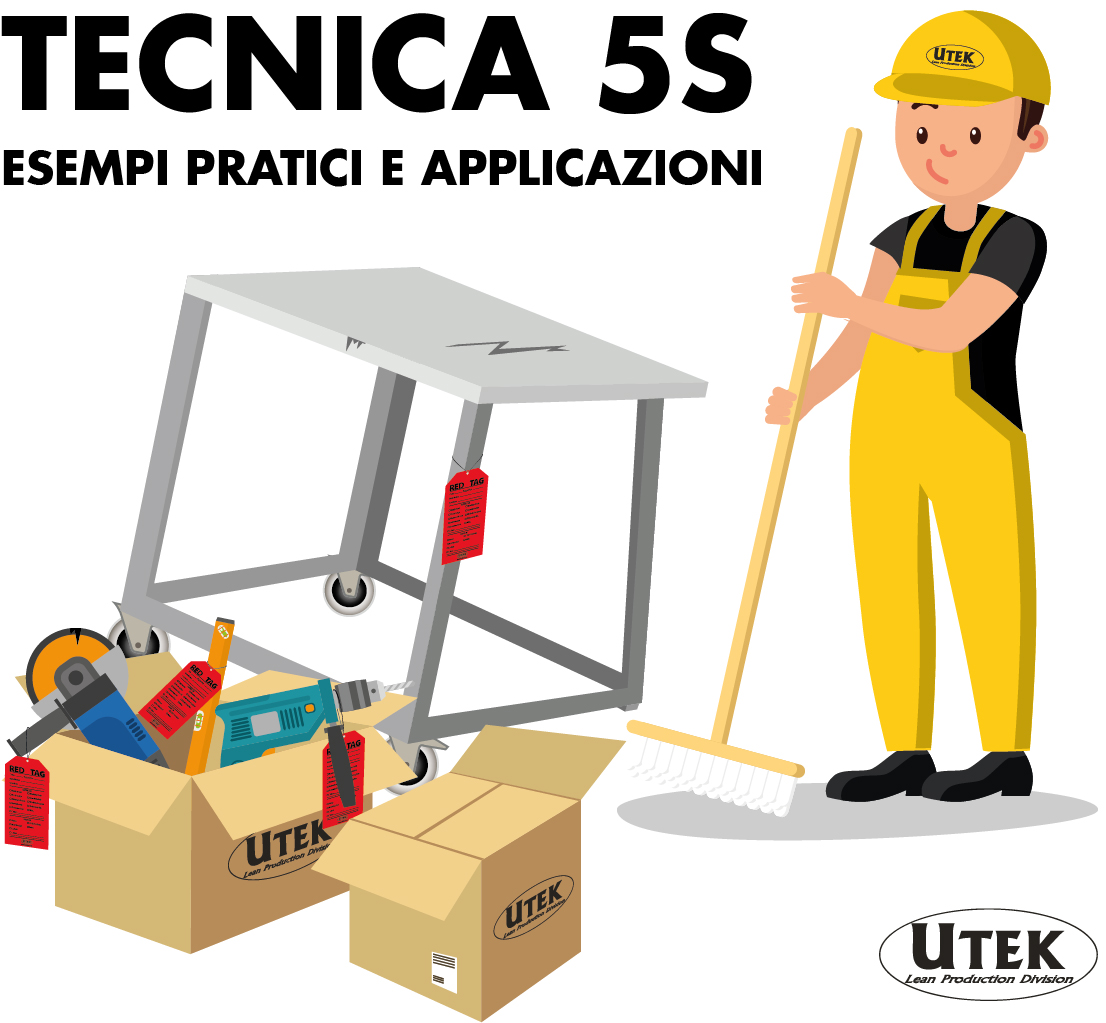
Il termine 5s si riferisce a una procedura organizzativa che permette di gestire in modo efficace la postazione di lavoro. Il nome indica le 5 procedure che consentono di ottimizzare, pulire e migliorare in termini di lean production e organization il luogo in cui si svolgono le attività produttive.
Indice dei contenuti
- Cosa sono le 5s
- 5s, come nasce il metodo
- A cosa serve il metodo 5s
- A cosa corrispondono le 5s
- Seiri - Separare
- Seiton – Mettere in ordine
- Seiso – Pulire
- Seiketsu – Standardizzare
- Shitsuke – Sostenere
- 5s o 6s: cosa scegliere?
- Benefici delle 6s
- 5s e Lean production
- Coinvolgimento dei dipendenti
- Applicare il metodo 5s in azienda
La tecnica 5s è alla base del concetto di Lean Manufacturing, la produzione snella. 5s è metodo sistematico per l’organizzazione dei luoghi di lavoro con obbiettivo aumentare i profitti diminuendo le spese. L'idea è nella tradizione giapponese del processo produttivo che prevede il raggiungimento della perfezione.
Questo avviene attraverso un ciclo continuo a discapito di un nemico ben noto a chi si occupa di questo tema: lo spreco. Quindi per raggiungere la perfezione della produzione, che i giapponesi chiamano kaizen, bisogna applicare delle tecniche. Come il ciclo di deming in azienda, che permette di definire le regole.
Si tratta di una tecnica di gestione visiva che enfatizza l'osservazione e il miglioramento del lavoro, utilizzando una mentalità in ottica Just in Time e strumenti specifici per creare valore e ottimizzare gli spazi di lavoro. Ma alla base di tutto questo c'è la tecnica delle 5s nel Lean Manufacturing, ovvero? Cosa significa?
5s cosa sono e a cosa servono?
Le 5s sono una combinazione di elementi che risiedono alla base di tutto ciò che oggi intendiamo come Lean Manufacturing. Sono una serie di pilastri che ti danno la possibilità di organizzare un processo produttivo attraverso la lente dell'efficienza, della riduzione di ogni spreco e della fluidità tecnica.
Come nasce il metodo delle 5s?
La tecnica delle 5s fonda le proprie origini nella tradizione giapponese, dalla scuola del Toyota Production System (dalla quale prende forma il Toyotismo) che ha fatto da apripista alla produzione snella. E raccoglie le tecniche messe a punto dalla stessa casa automobilistica, metodologie a lungo tenute segrete.
Perché erano la chiave del successo aziendale. A seguito del boom economico degli anni ‘80 le idee di successo iniziano a circolare e tramite un intenso scambio internazionale, giungono fino a Hiroyuki Hirano, che ne raccoglie i pilastri del lavoro visivo, dando i natali al concetto di 5S da noi oggi conosciuto.
Quali sono gli obiettivi del metodo 5s?
Abbiamo spiegato a grandi linee che cos’è il metodo 5s e da dove ha origine ma è giusto soffermarsi sul perché è vantaggioso applicarla. Un luogo di lavoro dove sono messe in pratica le 5s è di più facile fruizione. Gli spazi, gli strumenti e i materiali sono regolati da una logica e sono disponibili solo quando realmente necessario. A cosa serve il metodo 5s? Pulizia e organizzazione diventano una pratica comune e rendono i processi più sicuri ed efficienti.
5 pratiche chiave di questo metodo
Come suggerisce il nome, ci sono 5 punti che fanno la differenza quando si cerca una soluzione per applicare questa metodologia in una realtà aziendale. Le 5s rappresentano i 5 termini giapponesi simbolo dei passaggi di gestione visiva per organizzare qualsiasi tipo di azienda o catena di montaggio in ottica Lean.
Sono delle regole che possono dare risultati se applicate con attenzione. Quali sono? Affrontiamo i temi indicando sia il concetto giapponese che la traduzione in italiano. Mentre leggi i passaggi pensa a come questo sistema può essere implementato nella tua azienda e in altri aspetti della vita lavorativa.
Seiri – Separare
Devi separare ciò che serve da tutto ciò che è inutile. Però bisogna prendere prima coscienza di questo passaggio. Si tratta di svuotare un luogo molto disordinato e di classificare in tre gruppi ogni elemento prima di poter riposizionare in modo organizzato tutti i materiali all’interno della nostra “stanza”.
Esistono anche sistemi di codifica e catalogazione come: Etichette, red tag e segnaletica a colori, in grado di assegnare informazioni univoche a ogni materiale o prodotto. Devi immaginare di avere tre “scatole” con diverse destinazioni: Cose da gettare, da tenere o che devono essere sempre a portata di mano. Eliminare qualcosa che può essere funzionale alla produzione non è un bene, per questo bisogna ragionare sulla separazione e poi passare ai punti successivi.
Seiton – Mettere in ordine
Dopo aver separato l'utile dall'inutile, nella filosofia 5s bisogna organizzare il tutto e trovare anche una soluzione per le vie di mezzo. Avendo eliminato molte cose senza un’utilità effettiva, lo spazio per riorganizzare il restante materiale sarà sicuramente maggiore, questo fattore non deve però farti disorientare.
Dovrai disporre ogni cosa seguendo un ordine logico legato alla frequenza di utilizzo, per prime le cose di scarso utilizzo e a seguire tutte le altre in ordine crescente. Questo comporta anche un occhio di riguardo verso l’ergonomia di presa che dovrà crescere proporzionalmente con l’utilizzo di un elemento.
Seiso – Pulire
Una volta riorganizzato lo spazio, è fondamentale pulirlo per evitare che lo sporco possa portare all’usura dei materiali o al rischio d'infortuni. L'inutile deve essere eliminato, l'utile si mantiene in ordine e con efficienza. Pulire - la terza S “Seiso” - non comprende solo eliminare lo sporco, rappresenta la manutenzione ordinaria di macchinari e strumenti che se tenuti male rischiano di vanificare il lavoro per tenere materiali e strumenti organizzati a portata di mano.
Seiketsu – Standardizzare
Dopo un attento processo di riorganizzazione, nelle 5s della lean productione e manufacturing è di fondamentale importanza creare uno standard al quale rifarsi ogni volta. Standardizzare le operazioni, anche se può sembrare noioso, è il modo per risparmiare tempo, limitare gli errori, ottimizzare il lavoro.
I processi elencati devono diventare step da ripetere periodicamente utilizzando strumenti di organizzazione come pannelli forati porta attrezzi, tool organizers in spugna e marcature del pavimento. Se ogni cosa ha il proprio posto ed è possibile tracciarla, si possono assicurare standard organizzativi ripetibili.
Shitsuke – Sostenere
Completato il processo delle prime 4S non ci si può aggrappare per sempre ai risultati ottenuti da questa prima riorganizzazione interna. Priorità, spazi, operatori e standard cambiano e per non cadere nelle vecchie abitudini è fondamentale sostenere e investire sull’implementazione di nuove pratiche.
Lavora perché questo principio sia diffuso in ogni angolo della tua azienda. Non deve essere un principio noto solo a te o alla dirigenza: ogni individuo che fa parte del tuo mondo aziendale dovrà rispettare e accettare, ma anche mettere in pratica, le regole. La mentalità 5s è un’abilità che si assorbe con il tempo e che solamente una volta sviluppata come autodisciplina nella cultura dei dipendenti, può diventare una pratica comune, sostenuta quotidianamente.
Metodologia 5s o strategia 6s?
Il metodo delle cinque esse (5s) ormai è molto conosciuta perché consente di ridurre gli sprechi e migliorare l’efficienza produttiva. Tuttavia oltre alle tecniche e alle strategie delle 5s, ormai comunemente riconosciute, esiste anche una sesta S che rappresenta la sicurezza a livello aziendale.
Si tratta di un argomento che divide le persone in due correnti di pensiero, c’è chi pensa non sia necessario creare un punto a sé per la sicurezza perché è già sottintesa i tutte le 5s e chi al contrario sostiene che la sua presenza così significativa ne obblighi la creazione. Qualunque sia la posizione che decidi di abbracciare, ti rendi conto di quanto la sicurezza giochi un ruolo fondamentale in ogni aspetto che aziendale, processi sicuri sono processi efficienti.
Disporre il layout del tuo magazzino in modo logico, organizzare strumenti e materiali e pulire con regolarità, facilita il lavoro a tutti i tuoi collaboratori in azienda o all'esterno. Che possono completare la propria mansione senza inciampare, scivolare o incorrere in altre tipologie di lesioni ergonomiche.
Benefici 6s
Tempo
Incidenti o infortuni causano interruzioni di lavori, bloccaggio di macchine e in alcuni casi addirittura della linea produttiva intera. A seconda dell’entità della lesione esiste l’eventualità che per un lasso di tempo non precisato, manchi della forza lavoro che causa ulteriori perdite di tempo e aumento d'inefficienza.
Falle nel sistema e costi extra
Quando qualcuno si infortuna sul lavoro ha bisogno di prendersi del tempo di malattia. La mancanza di una persona spesso costringe a cercare un sostituto temporaneo che richiede formazione e più tempo per svolgere la propria mansione. Inoltre per alcune tipologie di infortunio è previsto un risarcimento,
Ossia un ulteriore costo extra da sostenere oltre a quello del sostituto. Al momento del rientro del dipendente in malattia, bisogna tenere in considerazione l’eventualità che non si sia completamente ristabilito e pertanto le sue prestazioni non siano più quelle di una volta, andando a intaccare l’efficienza del lavoro.
La sicurezza influisce sull’organizzazione
Quando si garantisce la sicurezza sui luoghi di lavoro lavori sull’organizzazione aziendale. Basti pensare alle marcature a terra utilizzate per delimitare le aree di passaggio per mezzi e pedoni. Oltre a evitare incidenti causati da interferenze, si assicura uno scorrimento del lavoro più fluido e pertanto più veloce.
Sicurezza è fiducia
Se procedi in totale sicurezza, puoi lavorare in maniera più spedita ed essere produttivo. Quando un dipendente è consapevole che la propria sicurezza è un aspetto importante e che tramite diverse misure viene tutelata e assicurata, dà fiducia all’azienda e lavora serenamente e con un ritmo più sostenuto.
Ispezioni
Se una struttura di lavoro non rispetta le norme di sicurezza nelle attività quotidiane rischia di ricevere ripetuti controlli dagli enti preposti, causa d'interruzioni e cali della produttività. Attivare tutte le misure necessarie alla sicurezza consente di ricevere meno ispezioni dalle autorità e ottenere esisti positivi.
5s e Lean production, cosa sapere?
Quando si fa riferimento ala produzione snella compare il termine 5s. Implementare un’organizzazione 5s implica snellire il lavoro permettendo di muoversi meglio. 5s è il punto di partenza per le altre pratiche di produzione snella come il kanban o Kaizen: così i luoghi di lavoro sono già organizzati e ripuliti.
5s per il coinvolgimento dei dipendenti
Per un’implementazione 5s di successo, il coinvolgimento dei dipendenti è la base. Essendo coloro che lavorano quotidianamente sul campo, sanno individuare più rapidamente i problemi e gli sprechi e pertanto a loro spetta il compito di prendere le decisioni nella fase “Separare” (Seiri).
Senza un percorso d'istruzione alle 5S si rischia di rimanere attaccati a un metodo solo teorico, una sorta di filosofia di lavoro fine a sé stessa. Le 5s devono essere uno strumento molto utile nel quale credere perché in grado di portare il lavoro di tutti ad alti livelli di efficienza, qualità e flessibilità.
Come applicare il metodo 5s in azienda?
Impossibile rispettare ogni passaggio in modo da avere un meccanismo perfetto, ci sarà sempre qualche falla o punto meno sviluppato. Alcuni processi sono complessi, soprattutto per le aziende di grandi dimensioni, ecco perché entrano in gioco gli strumenti della Lean Manufacturing e Organization.
Quando si decide di avviare un processo 5s bisogna formare e coinvolgere i dipendenti occupando ore che vengono momentaneamente sottratte alla produzione. Questo rallentamento del lavoro deve essere visto come un “investimento” temporaneo che avrà un ritorno non appena le 5S daranno i propri frutti.
Questo ha un'utilità limitata se non viene accompagnato da uno studio delle procedure da mettere in campo per applicare il metodo 5s. Per assicurarti il successo del processo di riorganizzazione 5s dovrai investire in mezzi che ne favoriranno il buon esito. Qualche esempio concreto preso dal catalogo Utek:
- Nastro a pavimento
- Stampanti di etichette
- Shadow board foam
- Pannelli forati
- Lavagne informative
- Carrello 5S
Dedicare tempo è l’unico modo per ottenere benefici dall’implementazione di soluzioni Lean. Forma i tuoi collaboratori e coinvolgili nel cambiamento tutelando la loro sicurezza. L’organizzazione 5s è il primo passo verso l’efficienza. Qualche indicazione in più? Chiedi informazioni all'ufficio vendite: info@utekvision.com.