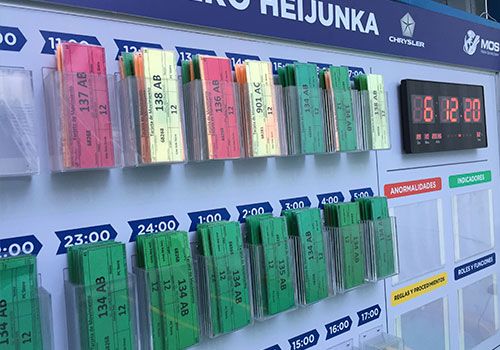
Il Kanban è un metodo di gestione dei processi produttivi che si basa soprattutto sulla comunicazione visiva, in grado di gestire il flusso continuo e il controllo del lavoro in corso. Questo sistema è stato sviluppato dalla Toyota negli anni '40 e il termine Kanban deriva dalle parole giapponesi kan (visuale) e ban (carta o scheda).
Indice dei contenuti
- Cos'è il Kanban? Una definizione
- Principio di funzionamento del Kanban
- Storia del metodo Kanban in azienda
- Metodo Kanban e Lean Manufacturing
- Implementare un sistema Kanban
- Scaffale Kanban nel Supermarket
- Come è fatto un cartellino Kanban
- Requisiti per un sistema Kanban
- Scelta del contenitore Kanban
- Quanti tipi Kanban esistono?
Il kanban è uno strumento del Lean Manufacturing. Utilizzato per migliorare l'efficienza produttiva determinando cosa, quanto e quando produrre, sulla base di una domanda effettiva rispetto a una domanda prevista..
Il kanban è un elemento della tecnica Just In Time, che consente di lavorare attraverso la logica pull basato sul eliminazione degli stock intermedi e aiuta a ridurre i costi di produzione e il miglioramento continuo. Questo consente di ridurre gli elementi peggiori dal punto di vista della logica Lean: l'inutilità e lo spreco.
Spreco di cosa? Sovrapproduzione, trasportarti di materie che non servono nell'immediato, il movimento inutile dei lavoratori, spazio per lo stoccaggio che potrebbe essere utilizzato in modo diverso, la materia stessa che viene stoccata per molto tempo in un magazzino e che può deteriorarsi. O non essere più adeguata alla produzione.
Avere scorte inutili, per molto tempo, rappresenta una perdita. E la tecnica che puoi mettere in campo con il kanban aiuta a risolvere questo problema. Mettendo in campo i passaggi virtuosi della Lean Organization.
Perché è così importante affrontare questo tema dopo aver toccato argomenti come il Ciclo di Deming (PDCA) e i principi della produzione snella? Continua a leggere per approfondire questo tema chiave del Lean Management.
Definizione tecnica di Kanban
Kanban è un termine Giapponese, significa (Kan 看 visuale, Ban 板 segnale), è molto più di un modello produttivo. Affinchè il kanban sia efficace utilizza strumenti specifici. Al centro c'è il “Cartellino”, componente chiave del sistema organizzativo da posizionare sul materiale da monitorare con una gestione visuale del flusso produttivo.
Questo ci dice poco sull'utilità nel processo organizzativo aziendale. Ma di cosa parliamo esattamente? Il kanban può avere forme diverse, dal cartellino cartaceo nella busta protettiva, al digitale o il contenitore.
Alcune aziende utilizzano bandierine o colonnine luci di segnalazione per indicare l'esaurirsi delle scorte. Uno dei più usati è il kanban fisico del cartellino: facile da implementare e visualizzare rispetto a un sistema ERP digitale. Il kanban ti aiuta a rendere l’ambiente di lavoro più visuale. Possiamo classificare tre versioni di Kanban.
Cartellino kanban
Una scheda di carta collegata a un contenitore che consente di capire in tempi rapidi cosa serve in un determinato momento, viene utilizzato per segnalare la necessità di attivare un ordine di prelievo o di produzione. Nella produzione a lotti si attende una determinata raccolta di cartellini prima d'iniziare il lotto successivo.
Contenitori kanban
In questa tipologia di metodo Kanban per semplificare e ottimizzare i processi produttivi, registriamo lo stesso utilizzo del cartellino kanban. Quindi, il contenitore dove è posizionato il materiale è il vero kanban.
E-Kanban
Il progresso ha permesso di passare dal cartellino fisico al sistema elettronico, dove i codici a barre vengono riportati sui prodotti, materiali o nelle posizioni. Questi barecode vengono scansionati per ricevere il materiale, questo segnale arriva direttamente al personale dedicato al riempimento. Alcuni sistemi genero addirittura un email quando vengono scansionati che inviano ordini a fornitori esterni o al buyer aziendale.
Per un approvvigionamento automatizzato del materiale alle stazioni di lavoro e nell'area intralogistica, le rulliere degli scaffali E-Kanban vengono dotate di sensori intelligenti per avere un rifornimento automatico.
Appena un contenitore (SLC) viene rimosso da uno scaffale kanban, un sensore wireless viene azionato, e invia una richiesta di rifornimento viene generata automaticamente nel sistema di controllo del flusso.
Il sistema gestionale reagisce alla notifica di richiesta ordinando il materiale di rifornimento, ad esempio inviando un line runner automatico per consegnare allo scaffale in questione senza attività manuale.
La fornitura si basa sulle necessità. Per consentire forniture completamente automatizzate, i vantaggi delle soluzioni E-Kanban automatiche sono combinate con la mobilità dei veicoli a guida automatica (AGV).
Il sistema risultante si muove in maniera del tutto automatica all'interno dell'azienda, secondo il principio Milk Run, consegnando il materiale richiesto nel posto giusto al momento giusto (ecco un esempio in basso).
br />
Mentre l’E-Kanban è diventato più diffuso, il cartellino kanban non è affatto obsoleto. In effetti in molte aziende utilizzano i cartellini fisici a supporto del E-Kanban. Il cartellino tradizionale genera un segnale evidente che informa i lavoratori su una specifica necessità, individuando più facilmente problemi sulle forniture.
Grazie al metodo kanban puoi rendere l’ambiente di lavoro più visuale migliorando la comunicazione tra produzione e magazzino in modo preciso. Nessuna improvvisazione e zero spostamenti inutili: grazie a questa soluzione tutto diventa più efficiente e flessibile. A favore del Kaizen, vale a dire il raggiungimento della perfezione.
Come funziona il metodo Kanban
In genere, le schede kanban contengono diverse informazioni, codice articolo, produttore, quantità di riordino, reparto, posizione di asservimento e codice a barre. Solitamente i cartellini kanban possono avere colori evidenti vengono posizionati in punti visibili sul Rack o sul contenitore dedicato al componente.
L’operatore preleva i componenti svuotando il contenitore e trova il cartellino e lo mette in una cassetta porta kanban in attesa del riordino. Quando l’operatore vede uno o più cartellini sa già esattamente cosa fare, innesca un azione ed elimina la necessità d'inutili domande al supervisore, deve ripristinare le scorte.
La scheda kanban in questo esempio funge da collegamento tra due reparti, i materiali e i loro processi. Chiaramente l'introduzione dei kanban, vale a dire degli elementi comunicativi efficaci, è inutile se alla base non c'è un'intenzione chiara e una pianificazione professionale dei flussi all'interno del magazzino.
Da dove nasce il sistema Kanban
Il kanban è stato introdotto da Taiichi Ohno nei cicli produttivi della Toyota Motor Company a metà del XX secolo. Ohno era interessato a un sistema PULL, ha esaminato le tecniche di gestione utilizzate dai supermercati americani e ha constatato la precisa previsione di vendita dei prodotti e delle scorte che avrebbero dovuto rifornire.
Toyota dal suo studio dei supermercati ha sviluppato il sistema di stoccaggio degli scaffali. Ora la tecnica è utilizzata non solo nei supermercati alimentari o nei processi produttivi Toyota, ma può esser utilizzata ovunque. E' stato implementato negli ospedali e nelle catene di fast food come processi First In First Out (FiFo).
Kanban e Lean Manufacturing
Il sistema di produzione Toyota ha ispirato industrie e processi produttivi. In molti paesi, questo sistema è conosciuto come Lean Manufacturing, che mira a identificare ed eliminare gli sprechi dai processi produttivi.
Eliminando gli sprechi, una azienda dedica tempo solo alle attività che aggiungono valore per il cliente finale. La produzione snella cerca di eliminare tre tipi principali di sprechi, chiamati 3M: Muda, Mura e Muri.
- Muda è lo spreco più elementare, di base. È tutto ciò che non aggiunge valore al prodotto finale. 7 principali Muda sono: difetti, sovrapproduzione, movimenti inutili, trasporti, lavoro extra, attesa, scorte.
- Mura, le irregolarità nel processo di produzione in azienda. Mura si verifica quando persone e materiali non sono gestite in modo appropriato. Si traduce in picchi di produzione, frequenti arresti e partenze.
- Muri, sono il sovraccarico costante da limitare nel tempo per aumentare la produttività interna grazie al metodo kanban. Questo può causare sforzi, lesioni, difetti, guasti e a lungo termine diventa insostenibile.
Kanban e JIT sono tool importanti in un ambiente di Lean Manufaturing: possono aiutare a eliminare molti di questi sprechi, rendendo la produzione più uniforme, riducendo le scorte ed eliminando la sovrapproduzione.
Come attivare un sistema Kanban
Se vuoi implementare questo sistema organizzativo hai delle linee guida da seguire. Coinvolgi tutti i membri dello team, organizza un incontro fornendo un’introduzione alla tecnica, come verrà utilizzata e come funzionerà.
Analizza il calcolo dei consumi, i metodi di riordino e le esigenze di rifornimento di ogni componente. Potrebbero esserci prodotti che non richiedono un rifornimento costante, quindi non sarebbe necessario unirli al sistema. Tuttavia ci potrebbero essere articoli con breve scadenza da tenere in considerazione. La formula:
Consumo orario Co: (3600 / Tc) x Nc
3600 sono i secondi in un ora
Tc è il tempo ciclo in secondi
Nc è la quantità di componenti utilizzata in ogni ciclo.
Consumo turno Ct: Co x 8h (ipotizzando turni di 8h)
Co è il consumo orario
Quanti contenitori per componente?
Cerca di standardizzare con cassette KLT o euro standard. Una volta calcolato il consumo di ogni componente possiamo decidere quanti contenitori per turno devono essere presenti. Teoricamente è sufficiente utilizzare una formula arrotondata per eccesso, ma è preferibile valutarlo di caso in caso.
Quantità contenitori Qc: Ct / Qi
Ct è il consumo per turno
Qi è la quantità contenitore
Sappiamo quanti contenitori per ogni codice portare in linea o sul supermarket per ogni turno. Portarli a inizio turno sarebbe un errore, potremmo avere dei componenti che creano disordine e comporterebbero troppi movimenti dell’operatore dalla postazione. Suddividiamo il rifornimento delle linee più volte al turno. Come?
Quantità contenitori oraria Qch: Qc / 8h
Qc è la quantità di contenitori per turno
Abbiamo la quantità di contenitori per ogni ora di produzione. In base agli spazi e alla disponibilità del personale per i rifornimenti decidiamo la frequenza di approvvigionamento kanban della linea calibrando tempi di ripristino uniformi in modo cadenzato. Solitamente la frequenza di rifornimento va dalle 2 alle 4 volte.
Scaffale Supermarket con il metodo kanban
Una volta calcolato correttamente il kanban possiamo procedere a progettare il magazzino supermarket dimensionandolo e posizionandolo vicino alla linea dove riporre i materiali. Dobbiamo disporre ogni codice diviso per corsia e identificandole correttamente sia dal lato di carico che dal fronte di prelievo.
Ogni corsia deve contenere una porta etichette: utilizza un flowrack a gravità, ti aiuterà a gestire FIFo i componenti. Tieni presente le altezze massime e minime per l’ergonomia. Tornando al dimensionamento dello scaffale tieni presente una scorta di sicurezza oltre al materiale necessario per la frequenza.
Ora dobbiamo trovare un modo per segnalare al operatore quando approvvigionare il materiale. Metti in pratica un sistema di tracciamento delle scorte per indicare il riordino dei materiali, dalla cassetta di raccolta kanban, al codice a barre o l'E-Kanban che invia in automatico la richiesta di approvvigionamento materiale.
Come è fatto un cartellino Kanban
Il punto da considerare quando affrontiamo il metodo in esame: cosa serve per un processo di movimento o di produzione? Dobbiamo pensare a quali informazioni riportare nel nostro cartellino kanban da inserire nel flusso.
Quali informazioni devi indicare? Hai spazio limitato, usalo per le informazioni necessarie. Ricorda che deve essere leggibile, le informazioni più importanti devono avere un carattere maggiore e di facile lettura.
Esistono kanban di prelievo o movimentazione, su un ordine di prelievo si suddividono in semplice o fornitore. Il Kanban semplice si utilizza per movimentare materiale verso un processo, le informazioni necessarie:
- Codice, è l’informazione più importante, l’identificativo deve essere univoco (stringa alfanumerica).
- Descrizione di cosa si trova nel contenitore.
- Quantità, dovresti annotare il numero di componenti che questo kanban rappresenta. Ti consiglio di utilizzare contenitori dimensionati alla quantità del kanban. Ricorda d'indicare l’unità, pezzi, confezioni, grammi.
- Ubicazione in cui si trova.
- Numerazione progressiva, è molto utile numerare il tuo kanban. Se hai 10 cartellini per un componente è bene numerarli da 1 a 10.
- Immagine, non è molto comune, ma se c’è spazio includere un immagine del componente sul cartellino aiuta.
- Imballo, indica il contenitore utilizzato.
I kanban fornitore servono come ordine di prelievo dal magazzino e devono riportare, in aggiunta al kanban semplice, il fornitore, da dove viene il materiale - può trattarsi di un interno come magazzino o da esterno - destinazione, allo stesso modo dove va il materiale, e ciclo di consegna con i metodi di fornitura.
Kanban di produzione è il collegamento diretto con la produzione. Si suddivide in kanban tradizionale e kanban segnale. Il kanban tradizionale è un ordine di produzione e contiene le seguenti infomazioni nei suoi spazi:
- Codice univoco;
- Descrizione di cosa si trova nel contenitore;
- Quantità: numero di componenti nella cassetta;
- Lavorazione (es. Montaggio, taglio, maschiatura ecc…).
Il kanban segnale è un cartellino posizionato nel contenitore che indica il livello di riordino.
- Lead Time, è da tenere in considerazione nel dimensionamento dello scaffale per ripristinare le scorte.
- Codice a barre, nella forma classica è in grado di memorizzare maggiori informazioni. In questo caso con un lettore scanner semplifichi notevolmente il trasferimento delle informazioni dal cartellino al sistema ERP.
-
Colori, puoi creare schede colorate utilizzando le buste porta kanban per distinguerle in caso ci siano più linee di produzione da gestire nello stesso reparto o priorità. Importante, evita di riportare dettagli.
Requisiti per un sistema Kanban
Per applicare un sistema kanban efficace devi rispettare alcuni requisiti:
-
Formazione e training agli operatori sull'utilizzo della tecnica e sulle regole della gestione visuale.
- Fornitori affidabili e lead time, tieni in considerazione la posizione del fornitore, i lotti minimi e imprevisti.
- Processi ripetibili, monitora l’efficienza di attrezzature e macchine con attività di TPM e 5S.
- Bassa variazione di prodotto con gestione a magazzino delle scorte per il kanban secondo il Just in time.
- Ordini regolari continuativi semplificano l’efficienza del kanban, tramite il livellamento della produzione. Al di fuori di questi requisiti non è impossibile implementare un kanban ma dovrai dedicarci maggiore attenzione.
Scelta del contenitore industriale
Il contenitore è un elemento del sistema kanban, valuta il più opportuno secondo diversi aspetti. Ad esempio: come viene movimentato? Manualmente o in automatico? Deve essere sollevato tramite dispositivi di presa?
Dove viene posizionato? Su carrello o su scaffalatura? Com’è il prelievo dei componenti? Il contenitore deve garantire la protezione dei pezzi durante il trasporto? Cerca di standardizzare con meno varianti possibili, semplificherai la gestione in magazzino e lo sviluppo delle postazioni di lavoro e delle linee di montaggio.
Quanti tipi di Kanban esistono?
I sistemi basati sul kanban sono usati continuamente in ambienti di produzione, uffici, magazzini e persino case. Ormai è un sistema con vantaggi comprovati nella riduzione delle scorte e nel miglioramento del efficienza produttiva. Di base si possono utilizzare diversi tools in supporto a un sistema kanban per garantire un corretto funzionamento basati sul principio dei segnali visivi. Le soluzioni che puoi trovare sono:
- Truck carts, carrelli progettati per il trasporto su camion, è un contenitore kanban. Movimentano il materiale dal fornitore alla linea di produzione senza manipolazioni o travasi. Il vantaggio dei Truck carts è la velocità di preparazione della spedizione, l'ergonomia e l’eliminazione della gestione degli imballi dalle linee.
- SAG Supermarket – scaffali a gravità a picking frontale ergonomici per la gestione scorte kanban. Si crea un flusso FIFO delle cassette sulle rulliere. I contenitori vuoti sono gestiti su un livello di ritorno a gravità inversa.
- Cassette abbattibili, contenitori pieghevoli in plastica offrono anche un'eccellente capacità interna e sono molto robusti. Ridurre al minimo lo spazio di stoccaggio da vuoti vuol dire ridurre i costi di spedizione di ritorno e gli spazi occupati in magazzino per la massima produttività ed efficienza.
- Tasche porta kanban, soluzione universale per aggiungere a qualsiasi contenitore, cassetta o pallet il cartellino kanban. Realizzate in materiale plastico per proteggere il cartellino da agenti esterni. Disponibili in vari colori per distinguerli in caso ci siano più linee di produzione da gestire nello stesso reparto o eventuali priorità.
- UT-Box minuterie, ideali per la fornitura salvaspazio ed ergonomica di piccole parti come dadi e viti. Sono montati su profili direttamente sul piano di lavoro. Protegge i componenti dagli agenti esterni. Il controllo è visibile, marcandolo con livelli di gestione della scorta lo rende un kanban segnale.
- Lavagna Kanban (detta Kanban Board), strumento di gestione visiva dei kanban, e dell'esposizione d'informazioni in modo visual. La modularità dei Kanban Box permette la realizzazione di soluzioni veloci e robuste per la disposizione di documenti con dimensioni da DIN A7 a DIN A4.
- Identificazione pallet - Le tasche kanban consentono d'inserire il cartellino al blocchetto laterale o centrale dei pallet in modo rapido e semplice da rendere identificabili questi elementi per il trasporto di materiali ingombranti. Sono ideali per l'etichettatura, specialmente quando le merci sono imballate e quindi non visibili.
- Contenitori VDA KLT, originariamente creati per il mercato automobilistico tedesco, sono diventati un packaging multi-purpose standard in tutte le industrie del mondo. Possono essere usate per la manipolazione intensiva, per la movimentazione manuale nelle linee produttive e il prelievo di componenti automatico dai contenitori. Ampia gamma di accessori per soddisfare le esigenze specifiche: coperchi, ripiani separatori o divisori ecc…
- Sensore wireless per scaffale E-Kanban per avere un rifornimento materiale automatico. Questo tilting sensor ha una staffa universale per il montaggio su rulliere disponibili in commercio, senza alcun attrezzo.
Ci sono altre soluzioni da adattare alla propria realtà. Con i fornitori esterni è possibile implementare un progetto di Lean Logistics con lo scambio dei contenitori vuoto per pieno per eliminare lo spreco di imballo e travasi.
Vuoi maggiori informazioni su questi oggetti? Per ulteriori domande e per scoprire come applicare il principio del metodo kanban alla tua azienda, contattaci all’indirizzo e-mail info@utekvision.com!