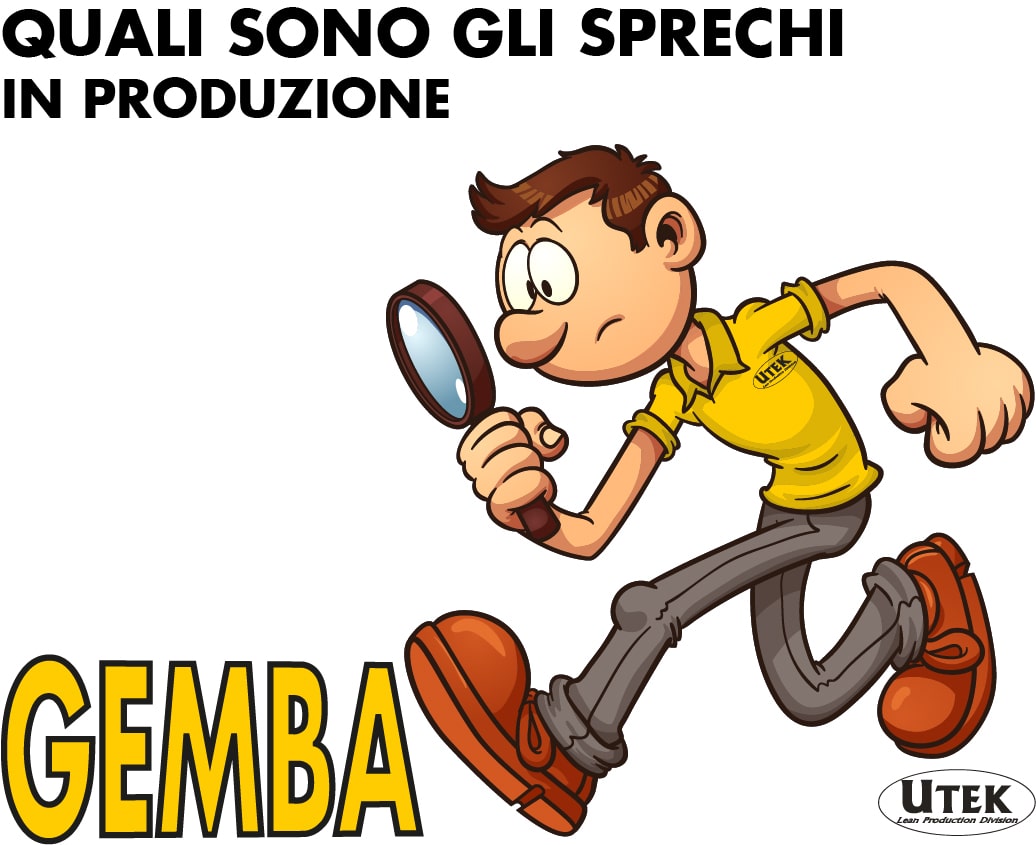
Indice dei contenuti
- 7 Modi per identificare ed eliminare i rifiuti Gemba
- T - Ridurre i trasporti e i movimenti
- I - Ridurre le scorte
- M - Limitare i movimenti
- W - Riduci i tempi morti
- O - Niente elaborazioni superflue e processi inutili al prodotto finito
- O - Eccessiva produzione rispetto alle richieste
- D - Individuare e limitare i difetti, scarti e i prodotti non conformi
- Raggiungere i risultati e limitare gli sprechi
Gli sprechi nella produzione sono nemici da combattere. L’obbiettivo principale di ogni azienda che affronta un processo produttivo è trovare una soluzione ai passaggi e frizioni che tendono a vanificare gli sforzi per poter creare valore per il cliente e ottenere un buon risultato in termini di profitto.
Questo lo ha capito la Toyota quando, in passato, ha gettato le basi per affrontare il tema della lean manufacturing, la produzione snella che punta verso un obiettivo chiaro: ridurre gli sprechi. Il tutto per raggiungere la perfezione, quello che in lingua giapponese viene identificato come kaizen.
Si tratta di un punto idealtipico, un obiettivo forse impossibile da ottenere in termini pratici, nella realtà. Ma che suona come dolce melodia per chi ha in mente l'ottimizzazione del processo produttivo. Soprattutto per i responsabili, per i dirigenti e per chi deve far quadrare i conti a fine mese.
Gli sprechi possono essere eliminati solo attraverso un processo di miglioramento continuo, messo in pratica da tutti i componenti aziendali in collaborazione.
Per avere un riscontro positivo da questo tipo di approccio, bisogna prima focalizzarsi su tre concetti fondamentali:
- Il flusso di valore: Tutti i processi necessari per portare il prodotto finito al cliente.
- Il valore: Tutto ciò che il cliente è disposto a pagare e dal quale può trarre beneficio.
- Gli sprechi: Perdite di tempo e risorse e che non portano valore al cliente.
Questi ultimi aprono una parentesi importante su un aspetto molto noto del TPS dal acronimo Toyota Production System, ovvero l’eliminazione dei tre mali del sistema produttivo 3M: Muda (sprechi), Mura (Irregolarità) e Muri (Sovraccarico).
- Muda: Rappresentano gli sprechi, elementi di più facile comprensione e individuazione. Significa eliminare il superfluo e tutte quelle attività che assorbono energie o tempo e che non creano valore.
- Mura: Rappresenta la variabile nel flusso di lavoro causata dall’irregolarità della domanda.
- Muri: Significa gestire il magazzino in ottica JIT (Just In Time), ovvero organizzando e allineando il magazzino e la produzione affinché ci sia sempre il giusto quantitativo di materiale quando serve e si evitino stock eccessivi.
Spesso l’eliminazione dei rifiuti viene ricondotta totalmente a Toyota ma si tratta di un concetto già toccato da Ford e prima ancora da Benjamin Franklin, dando credito all’idea che sia in circolo da quando esiste la produzione stessa.
Parlando di sprechi in produzione, si commette spesso la leggerezza di considerarli come tutto ciò che non porta valore aggiunto al cliente, senza soffermarsi sulla loro natura.
Bisogna pertanto distinguere tra spreco evitabile (che con impegno può essere eliminato totalmente) e spreco inevitabile (che può essere ridotto ma non eliminato), questa classificazione chiaramente però lascia libero spazio a tipologie di spreco non ben classificabili.
D'altro canto, anche se non si raggiungerà mai un equilibrio completo e totale, l'idea di ridurre gli sprechi abbracciando i principi della Lean Manufacturing è già un ottimo risultato. Prima però dobbiamo conoscere da vicino gli sprechi. Di cosa stiamo parlando? Quali sono? E come riconoscerli?
7 Modi per identificare ed eliminare gli sprechi in produzione
Gestire una produzione Lean richiede una certa attenzione nell’eliminare gli sprechi e per farlo ci viene in aiuto il Sistema Gemba (Termine giapponese che significa “Il luogo reale”).
Questa tecnica spinge a compiere una “camminata” (Gemba Walk) nella propria azienda alla ricerca dei “rifiuti”.
Osservare dal vivo il workflow permette di individuare più facilmente gli sprechi ma non sempre la loro natura li rende visibili a un primo sguardo. Per facilitarti nella loro individuazione, ti consiglio di ricordarti la parola “TIM WOOD”, ossia l’elenco di tutte le iniziali dei 7 Muda in inglese.
T = Transportation
I = Inventory
M = Motion
W = Waiting
O = Overprocessing
O = Overproduction
D = Defects
T - Ridurre i trasporti e i movimenti
Per ridurre al minimo gli sprechi da trasporto, le strade possono essere solo due: Ridurre le distanze da percorrere avvicinando le postazioni e disponendole in serie oppure rendere il trasporto più sicuro utilizzando sistemi di segnaletica orizzontale e di visual management per delimitare le zone a rischio e segnalare i percorsi da seguire.
I - Ridurre le scorte
Avere più materia prima in magazzino non vuol dire essere prudenti ma sprecare risorse inutilmente. In prima analisi richiedi uno spazio che puoi utilizzare diversamente e una manodopera specializzata che dovrà processare, gestire e sistemare le scorte che siano materie prime, WIP o prodotti finiti. Implementare una gestione just-in-time delle merci e delle lavorazioni consente di avere a disposizione il materiale necessario a un determinato processo, nel momento giusto e nel quantità richiesta. Si riducono così le scorte a inventario e le quantità di prodotti finiti stoccati a magazzino e in attesa di essere consegnati/venduti.
M - Limitare i movimenti
Limitare i movimenti non necessari contempla l'operazione di macchine e uomini intorno a un'operazione. Per ridurre i movimenti è importante seguire un piano costante per la manutenzione delle attrezzature che ne assicureranno una maggiore longevità e un funzionamento ottimale.
Inoltre seguire pratiche di sicurezza ergonomica consente ai lavoratori di limitare le movimentazioni inutili e pericolose, causa di possibili infortuni, lesioni o danneggiamenti.
W - Riduci i tempi morti
Un buon programma del workflow che unisca le tempistiche del processo umano con quello dei macchinari, consente di bilanciare i processi lavorativi, eliminando quasi totalmente i tempi di attesa in entrambi i sensi. Le attese causano anche il congelamento di capitale investito che non ha ancora prodotto un ritorno.
Un operaio non deve attendere la disponibilità di un materiale, come un macchinario non deve restare fermo o inutilizzato perché i processi precedenti non sono ancora stati conclusi.
O - Niente elaborazioni superflue e processi inutili al prodotto finito
Spesso per essere maggiormente allettanti sul mercato, si tende a utilizzare risorse più costose del necessario, realizzare più varianti di un prodotto o dare la possibilità di avere più funzioni, anche quando queste non aggiungono valore. Se queste caratteristiche sono espressamente richieste e garantiscono un ritorno paragonabile all’investimento, il tutto è accettabile, ma se l’elaborazione eccessiva nasce da un nostro eccesso di zelo, allora è necessario ricordarsi cosa il cliente cerca veramente e che i processi non richiesti sono fonte di spreco.
O - Eccessiva produzione rispetto alle richieste
Una grande battaglia che trova sfogo in quella che è la richiesta di lavorare in termini pull e non push. Nel primo caso l'azienda richiede le materie prime solo quando ha le richieste in lavorazione. Di conseguenza limita il WIP, lo stoccaggio in magazzino, e i costi di gestione. Un eccesso di prodotti finiti è poi da smaltire e ti costringe ad abbassare i prezzi per cercare di rientrare più velocemente dei costi già sostenuti e limitare quelli di stoccaggio... Come limitare questo spreco? Ascoltando e prevedendo la domanda, in modo da produrre solo ciò che serve e senza lavorare inutilmente.
D - Individuare e limitare i difetti, scarti e i prodotti non conformi
Questo tipo di spreco è legato a un problema di produzione: Anche se in una struttura ben organizzata gli errori di produzione dovrebbero essere quasi nulli, un prodotto non conforme o con difetti, è considerato muda, vale a dire, in lingua giapponese, uno spreco. Se l’errore di produzione è salvabile, sarà necessario investire tempo e risorse per ripetere alcuni procedimenti e rilavorazioni, se invece il difetto è così grave da rendere il prodotto finito uno scarto, si incorrerà in un’ingente perdita con conseguenti costi e tempi per la rimessa in produzione da zero. Nello specifico di risorse, tempo e attività di controllo che a loro volta vengono considerate attività che non aggiungono valore al prodotto finito ma vengono imposte al processo per verifica degli standard promossi.
Raggiungere i risultati e limitare gli sprechi in produzione
Una risposta esiste: Saper individuare ed eliminare i rifiuti di produzione pianificando i flussi interni attraverso attrezzature pensate per organizzare il lavoro in termini di lean manufacturing. Restare focalizzati su ciò che è valore per il cliente e imparare ad essere flessibili di fronte al continuo mutare del workflow, assicura maggiore efficienza e produttività.
Un occhio allenato è in grado di individuare ed eliminare ogni tipo di spreco in produzione limitandone al minimo l’impatto negativo.
Questi suggerimenti dovrebbero spingerti a tenerti sempre aggiornato e a cercare un continuo miglioramento per la tua attività. A tal proposito c'è un intero catalogo Utek da consultare per portare in azienda:
- Scaffali Supermarket
- Carrelli AGV
- Sistema Modulare Lean
- Sistemi di trasporto
- Carrelli Dolly Milk Run
- Roll-Pallet
- Trolley porta pallet
- Sollevatori Industriali KLT-Lifter
- Mini Lifter Posizionatori
- Tool Organizers
- Tool Shadow Boards
- Profili di contenimento UT-Box
La regola fondamentale? Non improvvisare. Le attrezzature necessarie per ridurre il muda sono inutili se alla base non c'è un progetto di Lean Transformation. E la comunicazione visiva diventa superflua se non si pianificano le priorità. In ogni caso contattaci all'indirizzo info@utekvision.com per avere maggiori informazioni sulle attrezzature lean e sul tuo piano di Lean Manufacturing.