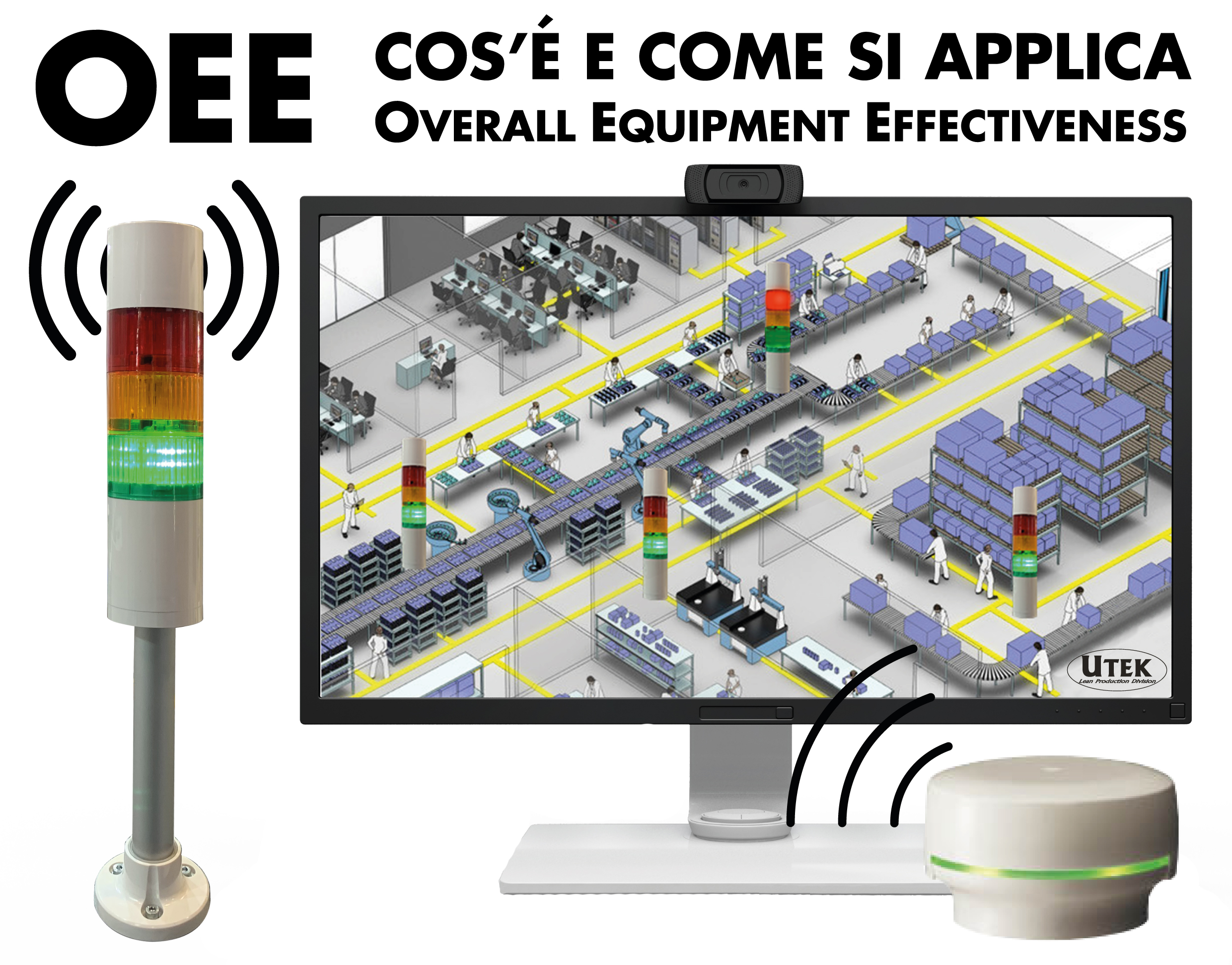
Indice dei contenuti
Il concetto di produzione snella si basa su un principio chiave che poi fa da matrice a tutto ciò che viene sfruttato in questo percorso: bisogna ridurre gli sprechi per dare posto al valore, a tutto ciò che ti permette di crescere e migliorare. Per poi ottenere un prodotto superiore da dare al cliente. In questo equilibrio si manifesta l'OEE, ovvero il tentativo di portare uno snodo della produzione - ad esempio un macchinario - alla sua massima efficienza. Cosa sapere in più rispetto a questo percorso?
OEE, Cos'è l'Overall Equipment Effectiveness
Cosa significa esattamente OEE? La definizione dell'acronimo è chiara: Overall Equipment Effectiveness. Per avere anche il significato basta una semplice traduzione e capiamo che stiamo parlando dell'efficacia generale dell'impianto. Si tratta, in buona sintesi, di una metrica utilizzata nell'ottimizzazione in chiave lean production per misurare l'efficienza delle performance dell’impianto.
Calcolando il valore dell’OEE siamo in grado di conoscere l’efficacia complessiva degli impianti, identificando le criticità che impediscono ai macchinari di produrre al massimo delle proprie capacità, ovvero alla massima velocità, senza perdite di tempo e di qualità, evitando di produrre prodotti non conformi a standard o che necessitano di essere rilavorati.
La misurazione dell’OEE è un’attività a beneficio di tutte quelle realtà che desiderano migliorare i propri processi lavorativi e aumentare le performance generali degli impianti.
Il procedimento alla base del calcolo e immagazzinamento d’informazioni dell’OEE, consente di ricavare un aggregato di informazioni per poter intervenire in modo mirato su singoli aspetti della produzione.
Origini Overall Equipment Effectiveness
Il primo a teorizzare l’OEE fu Seiichi Nakajima, padre del TPM, che nel 1988, nell’introduzione del suo libro sul Total Productive Maintenance, colloca lo standard internazionale di questo indicatore uguale o superiore all’85%.
L’OEE si calcola tramite la moltiplicazione di tre indicatori fondamentali: Disponibilità, Efficienza e Qualità.
Nakajima fornisce informazioni anche sullo stato ideale di ciascuno di questi fattori, posizionando il primo maggiore del 90%, il secondo maggiore del 95% e infine l’ultimo superiore al 99%.
Quali sono i parametri dell'OEE da rispettare
Si tratta di un valore che deve essere utilizzato per garantire una valutazione chiara degli standard qualitativi di una macchina, di un elemento decisivo del processo produttivo. A tal proposito è giusto definire che questa metrica si basa tre indicatori fondamentali per ottenere e calcolare la formula: Disponibilità, Efficienza e Qualità. Andiamo ad analizzarli insieme per capire cosa rappresentano, come calcolarli e come saranno parte del calcolo finale dell’Overall Equipment Effectiveness.
D - Disponibilità
Si tratta del tempo che un impianto è reso disponibile per la produzione. Ci possono essere dei momenti in cui l'elemento analizzato non si presenta come tale e questo porta a una perdita di tempo e di produttività: l'obiettivo è quello di essere sempre disponibili nel momento in cui c'è bisogno di una risposta. Questo parametro è noto anche come Available Time o Scheduled Time.
Si calcola facendo il rapporto tra il tempo operativo, cioè il tempo durante il quale la macchina è stata impiegata nel lavorare un pezzo, escludendo ogni forma di fermo e il tempo totale di produzione previsto, ovvero quello relativo al potenziale operativo massimo della macchina.
D = Tempo operativo / Tempo operativo previsto
Questo indice può essere anche calcolato come segue:
D = Uptime / (Uptime + Downtime)
Q - Qualità
La produzione avviene secondo norma? Ci sono standard da rispettare e la domanda posta da questo parametro è chiara: la produzione portata avanti dalla macchina è in grado di rispettare le esigenze? Esiste un parametro di riferimento che viene osservato? L'OEE si basa anche su questo, quella di valutare il numero nei prodotti conformi rapportato con la produzione totale.
Q = Numero pezzi conformi prodotti / Numero totale pezzi lavorati
E - Efficienza
Quali sono le prestazioni e i tempi di produzione? Un impianto deve essere presente e qualitativamente ineccepibile, però tutto questo deve essere eseguito in tempi ridotti. Quindi la terza voce per valutare un macchinario o un qualsiasi elemento del processo produttivo è quello dell'efficienza. Ovvero il tempo che serve a una macchina per concludere un ciclo di produzione a raffronto con quello previsto.
L’efficienza di produzione di una macchina dovrebbe essere un valore di facile riscontro ma anch’esso è soggetto a downtime ovvero a fermate di piccola o grande entità, causa di differenze tra la produttività reale e quella teorica.
Si calcola moltiplicando il numero di unità prodotte per il tempo reale, dividendo il tutto per il tempo operativo netto.
E = (Numero unità prodotte x Tempo reale) / Tempo operativo netto
Come calcolare l’OEE
Una volta imparati a riconoscere e a calcolare i 3 indici percentuali che compongono l’OEE, risulta chiaro il legame che li unisce, si tratta di valori sequenziali che procedono per eliminazione. Cerco di spiegarmi meglio.
Si parte dal tempo totale di produzione al quale dobbiamo sottrarre i fermi non previsti, arrivando così alla "Disponibilità".
Da questo valore togliamo le micro fermate e le perdite di efficienza in forma di tempo, ottenendo la "Produttività".
Infine eliminiamo il tempo sprecato per produrre materiale non conforme e arriviamo alla "Qualità".
L’Overall Equipment Effectiveness è il riassunto di tutto questo flusso produttivo che tocca i tre indicatori fondamentali che servono a calcolare l'efficacia di un impianto per poi scoprire dove si può migliorare anche grazie a un continuo processo di Deming. La formula classica per calcolare l'OEE e si traduce nella formula che segue:
OEE (Overall Equipment Effectiveness) = D x E x Q
Grazie a questa procedura di calcolo e all'analisi dei 3 fattori fondamentali che consentono d’identificare l'OEE si possono individuare le principali perdite per ogni settore preso in considerazione in modo da intervenire prontamente e mettere in pratica i pilastri della lean production: ridurre gli sprechi ed esaltare il valore.
Quali sono le 6 maggiori perdite monitorate?
Grazie al calcolo dell'OEE è possibile migliorare la propria produzione e le performance a essa connesse e difatti, grazie alle percentuali ottenute, siamo adesso in grado di pianificare e programmare operazioni d’implementazione e miglioramento per la nostra attività, per ridurre inefficienze e perdite.
In riferimento a tali operazioni salta fuori un nuovo termine, le 6 maggiori perdite per un impianto, tutte ricollegabili ai tre indicatori OEE.
A queste inefficienze è possibile porre rimedio con procedure a noi ormai ben note, frutto della Lean Production.
Riporto di seguito le 6 maggiori perdite raggruppate per indicatore e rimedio:
-
Disponibilità
- Guasti, fermi macchina non previsti – Risolvibile con un buon piano di manutenzione adeguata e preventiva
- Tempi di setup e aggiustamento della macchina – Velocizzare tali procedure per aumentare la disponibilità degli impianti
Questo primo focus riguarda l'ottimizzazione dei passaggi tecnici che si può tradurre in inconvenienti ma anche in fasi fisiologiche. L'obiettivo è quello di avere una manutenzione TPM tale da evitare il guasto nel momento in cui la produzione è in atto, ma anche quello di studiare un processo tale da per preparare la macchina senza perdere risorse preziose. In questi casi si lavora sul concetto di SMED, una metodologia per ottimizzare i tempi di preparazione alla lavorazione. Qual è il prossimo step relativo alle perdite da valutare?
-
Qualità
- Scarti e rilavorazioni – Correggere errori e problemi per limitare il numero di materiali non conformi a standard
- Tempi di startup – Limitare i tempi di produzione di una macchina non al massimo delle proprie capacità perché ad esempio ancora in fase di set-up
In alcuni casi la produzione registra delle perdite in termini di elementi non standardizzati, con difetti e sbavature. Questi casi, spesso, si verificano quando la macchina viene avviata e non è al massimo delle sue possibilità. Come ridurre tutto questo? Si tratta di un riavvio necessario? Bisogna lavorare sulle procedure operative con analisi FMEA ma anche sulla sua ottimizzazione Six Sigma in modo da produrre sempre il meglio ed evitare perdite di materia prima per creare prodotti inutilizzabili. Ultimo passaggio:
-
Prestazioni
- Arresti dovuti a inconvenienti - Ridurre i fermi anche brevi perché se sommati portano a un abbassamento sostanziale del rendimento dell’impianto
- Ridotta velocità di lavorazione, tempi di produzione non standard – Quando tali incongruenze diventano significative bisogna andarne a cercare le cause per poi porre rimedio a ciò che non ha funzionato.
Anche questo passaggio ci lascia intendere come una buona organizzazione interna ci può aiutare per aumentare le prestazioni e ridurre tutti gli scogli che possono creare ostacoli per l'ottimizzazione finale delle attività. Ad esempio, qual è la soluzione da mettere in pratica? Si può adottare un sistema di monitoraggio Andon o lavorare con delle applicazioni lean specifiche. Le soluzioni sono infinite, in questi casi puoi contattarci a info@utekvision.com per avere maggiori informazioni.